ผมจะนำเสนอหัวข้อดังกล่าวออกมาเป็นตอนนะครับ โดยเบื้องต้นผมจะนำเสนอบทนำที่เกี่ยวกับ การทดสอบแบไม่ทำลายกับงานวิเคราะห์ความเสีย ความสำคัญ วัตถุประสงค์ ข้อดี ข้อเสีย และเทคนิค NDT 9 ประเภทได้แก่
1. การตรวจสอบด้วยสายตา (visual Test)
2. การใช้สารละลายแทรกซึม (Penetrant Test)
3. การใช้อนุภาคผงแม่เหล็ก (Magnetic Particle Test)
4. การฉายด้วยรังสี (Radiography)
5. การใช้กระแสไหลวน (eddy Current Test)
6. การใช้คลื่นเสียงความถี่สูง (Ultrasonic Test)
7. การทดสอบการรั่ว (Leak Test)
8. การตรวจสอบด้วยคลื่นอะคูสติก (Acoustic Emission Test)
9. การถ่ายภาพความร้อน (Infrared thermography)
การประเมินผลจากการทดสอบแบบไม่ทำลาย (Nondestructive evaluation) มีศัพท์ที่เรียกกันหลายชื่อและรู้จักกันดีคือ nondestructive testing (NDT), nondestructive inspection (NDI) และ nondestructive examination (NDE) กิจกรรมนี้เกี่ยวข้องกับการประเมินผลที่ได้จากการทดสอบ การตรวจสอบอย่างละเอียดและการตรวจสอบทั่วไป โดยเบื้องต้นจะเกี่ยวข้องกับการตรวจดูหรือการวัดคุณลักษณะบางอย่างของวัตถุ บ่อยครั้งจะเป็นการตรวจสอบลักษณะบางอย่างของวัตถุว่ามีความผิดปกติ มีจุดบกพร่องหรือความไม่ต่อเนื่องหรือไม่ การตรวจสอบทั่วไป การตรวจสอบอย่างละเอียดและการทดสอบเหล่านี้จะใช้ในการค้นหารอยบกพร่องหรือความผิดปกติใดๆ ที่มีอยู่ในชิ้นงาน ทั้งที่เป็นอันตรายต่อการใช้งานหรือไม่เป็นอันตรายต่อการใช้งาน โดยที่ไม่ทำให้เกิดความเสียหายขึ้นกับชิ้นงานนั้น การประเมินผลจากการทดสอบแบบไม่ทำลายเป็นเครื่องมือที่มีความสำคัญที่ช่วยเพิ่มความปลอดภัย เพิ่มคุณภาพและความเชื่อมั่นของผลิตภัณฑ์ เพิ่มความสามารถในการผลิต ลดค่าใช้จ่าย รักษาสิ่งแวดล้อมและประหยัดเงิน
การทดสอบแบบไม่ทำลายอาจไม่ค่อยมีการประยุกต์ใช้กับงานวิเคราะห์ความเสียหายกันมากนักในบ้านเรา เพราะโดยส่วนใหญ่มักนำไปตรวจสอบหลังการผลิต ประกอบและติดตั้งก่อนการใช้งาน แต่หลังจากนำไปใช้งานแล้วเกิดความเสียหาย เทคนิคการทดสอบแบบไม่ทำลายกลับมีบทบาทน้อยมากในการเข้าเสริมเพื่อยืนยันสาเหตุที่แท้จริงของการเสียหาย อย่างไรก็ตามจึงถือเป็นโอกาสที่ดีเมื่อวิธีการทดสอบและการประเมินผล เช่น การใช้สารละลายแทรกซึม การทดสอบด้วยอนุภาคผงแม่เหล็ก การใช้คลื่นอุลตร้าโซนิค และการฉายรังสีที่ต้องการเพื่อให้งานตรวจสอบความเสียหายบรรลุผลสำเร็จ ในปัจจุบันนี้จะเห็นว่าหลายหน่วยงานมีการประยุกต์ใช้เทคนิคการตรวจสอบแบบไม่ทำลายมาใช้ในงานวิเคราะห์ความเสียหาย จากการประยุกต์ใช้ร่วมกันทั้งสองศาสตร์นี้ ทำให้ผลที่ได้จากการวิเคราะห์ความเสียหายนำไปสู่การกำหนดวิธีการทดสอบแบบไม่ทำลาย หรือค้นพบวิธีอื่นที่มีความเหมาะสมมากกว่า และเพื่อค้นหาเทคนิคการตรวจสอบแบบไม่ทำลายเพื่อดำเนินการวิเคราะห์ความเสียหาย เช่น การหาตำแหน่งเพื่อตัดชิ้นส่วนด้วยเทคนิคการฉายรังสี แต่น่าเสียดายการเชื่อมกันระหว่างการทดสอบแบบไม่ทำลายและการวิเคราะห์ความเสียหายมีการนำมาใช้เพื่อให้เกิดประโยชน์ร่วมกันน้อยมาก และถ้ามีการนำมาใช้ร่วมกันก็มักจบลงด้วยการขัดแย้งกัน นอกจากว่าท่านจะเปิดใจเท่านั้น
หลายครั้งเราจะเห็นว่ามีการเรียกร้องให้ทำการวิเคราะห์ซ้ำ เนื่องจากผลการตรวจสอบได้ชี้ให้เห็นว่าความเสียหายสามารถป้องกันไม่ให้เกิดได้โดยการทดสอบที่คลอบคลุมมากขึ้นหรือมีการดำเนินการทดสอบที่ละเอียดมากมากขึ้นกว่าเดิม หรืออาจเกิดจากผู้ปฏิบัติการทดสอบแบบไม่ทำลายสามารถชี้ให้เห็นได้ว่ารายงานผลการวิเคราะห์ความเสียหายไม่สามารถนำมาใช้ประโยชน์ได้เลยหรือมีการแปรผลผิดพลาดจากการผลการทดสอบ โดยยกตัวอย่างเกี่ยวกับปัญหาที่เกิดขึ้นดังนี้ มีการเสียหายของชิ้นส่วนเกิดขึ้นกรณีหนึ่งซึ่งได้มีการตรวจสอบด้วยเทคนิคที่ไม่ทำลายและดำเนินการวิเคราะห์ความเสียหายซึ่งพบว่าสามารถเอามาใช้ร่วมกันและไม่สามารถเอามาใช้ร่วมกันได้ โรงงานผู้ผลิตแห่งหนึ่งพบความเสียหายที่เกิดขึ้นอย่างต่อเนื่องในชิ้นส่วนที่มีความสำคัญมากอันหนึ่งสำหรับการขนส่งเข้าสู่กระบวนการผลิต ความเสียหายของชิ้นส่วนดังกล่าวนั้น นอกจากจะส่งผลให้สูญเสียการผลิตแล้ว ยังส่งผลต่อการสูญเสียชีวิตถ้าความเสียหายได้เกิดขึ้นในตำแหน่งที่เกี่ยวข้อง โดยในฐานะผู้ผลิตได้ตั้งคำถามขึ้นมาอย่างเพียงพอ ซึ่งผู้จัดการอาวุโสได้ให้ทีมงานภายในบริษัททั้งแผนกวิเคราะห์ความเสียหายและแผนกทดสอบแบบไม่ทำลายเขาดำเนินการเพื่อหาสาเหตุที่เกิดขึ้น ซึ่งโดยส่วนใหญ่ในโรงงานทั่วไป เราจะพบว่า ห้องปฏิบัติการโลหะวิทยาเป็นส่วนหนึ่งแผนกวิศวกรรม ในขณะที่กลุ่มทดสอบแบบไม่ทำลายมักเป็นส่วนหนึ่งฝ่ายซ่อมบำรุง โดยเมื่อความเสียหายเกิดขึ้นครั้งแรก ชิ้นส่วนดังกล่าวได้ถูกนำมาให้นักโลหะวิทยาตรวจสอบทันที ซึ่งเป็นผู้ทำการตรวจสอบในเบื้องต้น จากการตรวจสอบได้ชี้ให้เห็นว่าเกิดการแตกร้าวที่ตีนรอยเชื่อม (Toe Crack) ในส่วนของโครงสร้างที่ผ่านการเชื่อม อย่างไรก็ตามได้พบการดำเนินการวิเคราะห์ความเสียหายยังไม่สมบูรณ์ แล้วยังมาวินิจฉัยว่าความเสียหายเกิดขึ้นเนื่องจากจุดบกพร่องบริเวณแนวเชื่อมที่ผิว (Surface welding defect) และมีความน่าจะเป็นว่าไม่ได้เกิดจากการเชื่อม เพื่อรับประกันเรื่องดังกล่าวทางห้องปฏิบัติการทางโลหะวิทยาได้กำหนดว่าให้พนักงานทดสอบแบบไม่ทำลายทำการตรวจสอบหาลักษณะความไม่ต่อเนื่องของผิวหน้า โดยกระบวนการตรวจสอบชิ้นส่วนดังกล่าว (ด้วยสารละลายแทรกซึม) แสดงให้เห็นว่าไม่พบจุดบกพร่องที่ผิวหน้าแต่อย่างใดและและคิดว่าระบบดังกล่าวสามารถนำไปใช้งานได้ แต่หลังจากใช้งานได้ประมาณ 1 สัปดาห์ เมื่อมาตรวจสอบอีกครั้งพบว่าได้เกิดความเสียหายขึ้นมาอีก 2 ครั้ง ซึ่งเกือบเป็นอันตรายกับพนักงาน ลำดับขั้นตอนการเสียหายที่เกิดขึ้นครั้งนี้ได้เริ่มจากการรับแจ้งให้ทำการตรวจสอบซ้ำ เมื่อการตรวจสอบยังชี้ให้เห็นยังสามารถค้นพบเครื่องบ่งชี้ถึงจุดบกพร่องของวัสดุที่นำไปสู่การเสียหาย จึงได้มีการมองหาผู้วิเคราะห์จากภายนอกโรงงานมาช่วย จากการทบทวนข้อเท็จจริงที่ทางโรงงานเข้าใจหลังจากเกิดความเสียหาย 3 ครั้งและได้ทำการทดสอบ 2 ครั้ง ทำให้บางหัวข้อค่อนข้างจะชัดเจน กล่าวคือ การวิเคราะห์ความเสียหายห่างไกลความเป็นจริงมากและยังไม่สมบูรณ์และได้ลงความเห็นโทษกระบวนการเชื่อม และขยายไปถึงผู้ทดสอบด้วย มีข้อเสนอแนะว่าต้องดำเนินการทดสอบหาความไม่ต่อเนื่องที่ผิวหน้าอย่างเร่งด่วน ทีมงานวิเคราะห์ความเสียหายจากข้างนอกได้ชี้ให้เห็นว่าความเสียหายเกิดขึ้นเนื่องจากการล้าตัวในชิ้นส่วนที่ใช้งานมาแล้ว 15 ปี และจุดเริ่มต้นการแตกหักอยู่ภายใต้ผิวหน้า (subsurface) ลงไปเล็กน้อย และคาดว่ารอยแตกร้าวได้แยกผิวหน้าในช่วงเวลาก่อนที่จะเกิดการแตกหัก ดังนั้นการเลือกวิธีการทดสอบดังกล่าวของบริษัทจึงไม่ถูกต้องเหมาะสม เพราะว่าสารละลายแทรกซึมไม่สามารถตรวจหารอยแตกใต้พื้นผิวได้ ซึ่งจากส่วนการวิเคราะห์ของทีมที่จัดหาจากภายนอก พบว่าวิธีการที่เหมาะสมในการตรวจหารอยแตกใต้พื้นผิว คือ การทดสอบด้วยอนุภาคผงแม่เหล็ก จากผลการตรวจสอบอย่างละเอียดด้วยวิธีการทั้งสองและการวิเคราะห์ความเสียหาย กระบวนการซ่อมบำรุงต้องมีการปรับปรุงโดยการป้องกันไม่ให้รอยแตกที่ปรากฏอยู่รับแรงดึงจนกว่าจะมีการออกแบบใหม่เพื่อให้สามารถรับแรงแบบรอบได้ ในกรณีดังกล่าวนี้ สามารถกล่าวได้ว่า การเสียหายที่เกิดขึ้นครั้งแรกสามารถตัดปัญหาจากการเชื่อมออกไปได้ และทำการออกแบบใหม่ ความเสียหายที่เกิดขึ้นครั้งที่สอง เกิดขึ้นเมื่อนักวิเคราะห์ความเสียหายของบริษัทได้ดำเนินการอย่างรวดเร็วและเกิดจากการเลือกวิธีทดสอบที่ไม่เหมาะสม ครั้งที่สาม ความเสียหายเกิดขึ้นเมื่อทีมทดสอบแบบไม่ทำลายไม่ได้สอบถามว่าทำไมถึงต้องเลือกสารละลายแทรกซึมในการทดสอบ ซึ่งการทดสอบด้วยอนุภาคผงแม่เหล็กสามารถดำเนินการได้รวดเร็วกว่าและมีความสามารถตรวจสอบความไม่ต่อเนื่องที่ผิวและใต้ได้ดีกว่า จากเหตุการณ์ข้างต้นดังกล่าว ชี้ให้เห็นว่าทั้งสองทีมงานของบริษัทขาดความรู้ความเข้าใจอย่างลึกซึ้งในขั้นตอนการทดสอบเบื้องต้น จนนำมาสู่การเสียหายอีก 2-3 ครั้งตามมา กล่าวคือ ถ้าทีมวิเคราะห์ความเสียหายได้ดำเนินการอย่างถูกต้อง เช่น เมื่อตรวจสอบผิวแตกหักของชิ้นส่วนแล้วตรวจพบว่ากลไกความเสียหายเกิดจากการล้า ก็สามารถออกแบบใหม่เพื่อป้องกันปัญหาดังกล่าวได้ ยกเว้นรอยร้าวจากการล้าตัวได้ขยายมาจากจุดบกพร่องจากการเชื่อมบนผิวหน้า และในท้ายที่สุด การประยุกต์ใช้เทคนิคทั้งการทดสอบแบบไม่ทำลายและการวิเคราะห์ความเสียหายควบคู่กันจะนำไปสู่การแก้ปัญหาได้อย่างรวดเร็ว
สำหรับตอนต่อไปผมจะนำเสนอ "ความสำคัญของการตรวจสอบโดยไม่ทำลาย" โปรดคอยอ่านนะครับ............
สมัครสมาชิก:
ส่งความคิดเห็น (Atom)
การกัดกร่อนกับท่อทองแดงแบบรังมด (Ant-nest corrosion)
วันนี้มีเคสจากหน่วยงานขนส่งมวลแห่งหนึ่งแจ้งว่าท่อทองแดงในระบบเครื่องปรับอากาศเกิดการกัดกร่อนแล้วนำมาสู่การรั่วมาปรึกษา ผมจำได้ว่าเคยวิเคราะห...
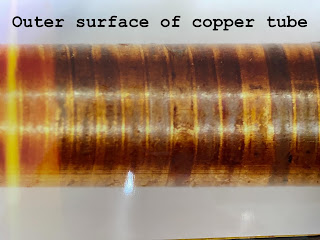
-
วันนี้เราเรียนรู้รูปแบบการเสียหายของวัสดุในรูปแบบถัดมา นั่นก็คือ การล้า หรือ Fatigue จะมีรายละเอียดเป็นอย่างไร เชิญติดตามได้เลยครับ คำว่า ...
-
cr : https://doi.org/10.1016/j.ijplas.2023.103601 เมื่อชิ้นส่วนโลหะถูกนำมาใช้งานภายใต้สภาวะอุณหภูมิสูงในขณะเดียวกันก็รับความเค้นแรงดึงไปด้ว...
-
วันนี้ผมขอนำเสนอรูปแบบการเสียหายของวัสดุแบบแรกนะครับ คือ การแตกหักแบบเปราะ การแตกแบบเปราะของวัสดุเกิดขึ้นเมื่อการกระทำของแรงทางกลมีค่าสูงก...
ขอบคุณสำหรับความรู้ครับทำต่อไปนะครับ
ตอบลบการตรวจสอบโดยไม่ทำลายนำมาใช้ครั้งแรกกับอะไรหรอคะ
ตอบลบ