ความเสียหายที่เกิดขึ้นกับชิ้นส่วนอุปกรณ์ของโครงสร้าง หรือเครื่องจักรเป็นปัญหาที่มักพบได้เสมอในอุตสาหกรรมประเภทต่างๆ แม้ว่าในปัจจุบันจะมีอุปกรณ์ช่วยในการออกแบบและมีการใช้เทคนิคในการซ่อมบำรุงที่ทันสมัยในการตรวจสอบสภาพการใช้งานของเครื่องจักรมากขึ้นก็ตาม แต่สภาวะการทำงานจริงของเครื่องจักรที่มักไม่เป็นไปตามที่ออกแบบไว้ ทำให้มีโอกาสที่ส่วนใดส่วนหนึ่งของโครงสร้างหรืออุปกรณ์จะรับภาระกรรมเกิน ซึ่งนำไปสู่การแตกหักเสียหายในที่สุด ความเสียหายที่เกิดขึ้นทำให้เกิดผลเสียทางเศรษฐกิจ สุขภาพ หรือชีวิต ดังนั้นจึงต้องมีการวิเคราะห์ความเสียหาย เพื่อลดความสูญเสียที่อาจเกิดขึ้นในอนาคต
การวิเคราะห์ความเสียหาย หมายถึง การวินิจฉัยหาสาเหตุที่แท้จริงของความเสียหายที่เกิดขึ้นสำหรับใช้เป็นแนวทางพิจารณาในการแก้ไข ซ่อมแซม หรือออกแบบใหม่ เพื่อป้องกันความเสียหายชนิดดังกล่าวที่อาจเกิดขึ้นในอนาคต
ขั้นตอนการวิเคราะห์ความเสียหาย
การวิเคราะห์ความเสียหายของชิ้นส่วนอุปกรณ์ต่างๆต้องเริ่มต้นจากประวัติหรือข้อมูลความเป็นมาของชิ้นส่วนที่เสียหายนั้นๆ เช่น ชนิดของวัสดุ ส่วนผสมทางเคมี ข้อกำหนดต่างๆ (Specification) กระบวนการผลิต การอบชุบ การอบชุบทางความร้อน ตลอดจนสภาวะการใช้งาน บางกรณีก็อาจจำเป็นต้องมีแบบของชิ้นส่วนที่เสียหายด้วยหากสามารถหาได้ นอกจากนี้หากสามารถทราบได้ว่าขณะที่ชิ้นส่วนเกิดความเสียหาย สภาวะแวดล้อม เช่น อุณหภูมิ บรรยากาศรอบๆเป็นอย่างไรอาจจะเป็นประโยชน์ต่อการวิเคราะห์ต่อไป
เมื่อได้รับชิ้นส่วนที่เสียหายแล้ว ต้องวางแผนการวิเคราะห์ทดสอบก่อนว่า ส่วนใดต้องนำมาทดสอบอะไร แล้วจึงทำการตัดชิ้นส่วนที่เสียหายไปทดสอบ การวางแผนต้องพิจารณาถึงความจำเป็นของข้อมูลเพื่อประหยัดเวลาและค่าใช้จ่าย และมีความยืดหยุ่นและพิจารณาลำดับขั้นของการวิเคราะห์ การเลือกตำแหน่งการทดสอบผิดจะไม่เกิดประโยชน์แต่อย่างได
เมื่อทราบข้อมูลเบื้องต้นเกี่ยวกับข้อมูลที่เสียหายแล้ว ขั้นตอนต่อไปในการวิเคราะห์คือ
1. บันทึกประวัติการทำงาน
ลำดับแรกควรสอบถาม หรือบันทึกข้อมูล รายละเอียดเกี่ยวกับประวัติการใช้งานของชิ้นส่วนที่เสียหาย เช่นการใช้งานในสภาวะปกติเป็นอย่างไร โดยอาจจะสอบถามถึง
• แรงที่กระทำเป็นแรงคงที่ เป็นรอบหรือแรงกระทำเกินขอบเขต(Overload) บ้างเป็นครั้งคราวหรือไม่
• อุณหภูมิการใช้งานมีการเปลี่ยนแปลงหรือไม่ หากมีการเปลี่ยนแปลง เปลี่ยนแปลงไปมากน้อยเพียงใด
เนื่องจากอุณหภูมิมีผลต่อการผุกร่อนของโลหะ หากชิ้นส่วนของโลหะนั้นอยู่ในสภาวะกัดกร่อน นอกจากนี้โลหะผสม เมื่ออยู่ในสภาวะที่อุณหภูมิสูงเป็นเวลานานๆ อาจทำให้จุลโครงสร้างเปลี่ยนแปลงไป หรือมีอนุภาคตกตะกอน(Precipitate) อยู่ตามขอบเกรน หรือในเหล็กกล้าที่มีจุลโครงสร้างเป็น Pearlite, cementite ที่เดิมเคยมีรูปร่างเป็นแผ่น (lamellar) อาจเปลี่ยนเป็นรูปกลม
ประวัติการใช้งานของชิ้นส่วนที่เสียหายที่สมบูรณ์ มีความสำคัญต่อการวิเคราะห์ความเสียหายมาก ซึ่งเป็นส่วนที่ช่วยให้การทำงานง่ายขึ้น และมีความมั่นใจในผลการวิเคราะห์ว่าเป็นไปในทางที่ถูกด้วย นอกจากนี้ประวัติการซ่อมแซมชิ้นส่วนที่เสียหายว่าเคยซ่อมเมื่อใด บ่อยหรือไม่ เหตุที่ต้องซ่อมแซมและวิธีการซ่อมเป็นข้อมูลที่ต้องบันทึกไว้ด้วยเช่นกัน
อีกสิ่งหนึ่งที่ต้องทำคือ ควรถ่ายภาพชิ้นส่วนที่เสียหายเอาไว้ทุกแง่ทุกมุม ก่อนที่จะนำชิ้นส่วนนั้นไปทำการวิเคราะห์ต่อไป
2. การตรวจสอบด้วยสายตา (Visual Inspection)
ชิ้นส่วนที่เสียหายทั้งหมด ควรได้รับการตรวจสอบด้วยสายตาอย่างละเอียด ก่อนที่จะมีการทำความสะอาด แล้วบันทึกเอาไว้เช่น หากพบว่ารอยแตกเก่ามีอยู่แสดงว่ารอยแตกเกิดขึ้นมาเป็นระยะเวลาช่วงหนึ่งแล้ว ก่อนที่จะเกิดความเสียหาย และรอยแตกอาจจะถูกพบมาก่อน แต่ไม่ได้ให้ความสำคัญเท่าที่ควร ลักษณะเช่นนี้ ควรบันทึกเอาไว้ด้วย
นอกจากนี้ลักษณะของรอยแตก สีของผิวที่แตกหักเสียหายเป็นอย่างไร รอยการแตกเริ่มมาจากทางใด
ขนาดของรูปร่างของชิ้นส่วนที่เสียหายควรบันทึกเอาไว้อย่างละเอียด หรืออาจจะใช้ภาพวาดหรือภาพถ่ายช่วย บางครั้งอาจจะต้องใช้กล้องกำลังขยายต่ำหรือแว่นขยาย
3. การเลือกตำแหน่งที่จะนำมาทดสอบ
ผู้วิเคราะห์ต้องตัดสินใจเลือกตำแหน่งในการตัดชิ้นส่วนที่เสียหาย เพื่อจะได้ตำแหน่งที่สามารถชี้บ่งถึง
สาเหตุการเสียหายได้ บางกรณีอาจต้องเปรียบเทียบชิ้นส่วนที่เสียหายกับชิ้นส่วนประกอบประเภทเดียวกันที่ไม่เกิดความเสียหายหรือจากชิ้นเดียวกันแต่ห่างออกไปจากบริเวณที่เสียหาย ทั้งนี้อาจจะสามารถชี้บ่งได้ว่าความเสียหายที่เกิดขึ้นเนื่องมาจากสภาวะการใช้งาน หรือจากกระบวนการผลิต เช่น ท่อใน Boiler เกิดความเสียหายหากมีโครงสร้างที่ต่างกัน แสดงว่าสภาวะการใช้งานทำให้จุลโครงสร้างเปลี่ยนแปลง ซึ่งอาจจะเป็นสาเหตุหนึ่งในข้อสันนิษฐานว่าสาเหตุของความเสียหายอาจเกิดขึ้นเนื่องจากการใช้งาน
4. การทำความสะอาด การตัด และการรักษาผิวหน้าที่เสียหาย
ผิวที่แตกหักเสียหายของชิ้นส่วนที่ต้องการวิเคราะห์ เป็นหลักฐานที่สำคัญอย่างยิ่ง ดังนั้นจึงควรรักษาสภาพผิวที่เสียหายไว้ เพราะผิวที่เสียหายอาจเป็นสนิมหรือเกิดออกไซด์เมื่อเก็บไว้ในบรรยากาศ หรืออาจจะลบเลือนไปจากการเสียดสีหรือกระแทกกับชิ้นส่วนอื่นๆ ขณะทำการเก็บตัวอย่าง หรือขนส่งได้ ที่สำคัญไม่ควรเช็ดผิวหน้าที่เสียหายด้วยผ้าเพราะอาจทำให้อนุภาคที่อยู่ที่ผิวหน้าหลุดไป ซึ่งอนุภาคเหล่านี้อาจจะเป็นสิ่งบ่งชี้ถึงสาเหตุความเสียหายได้ และการแตะผิวแตกหักด้วยนิ้วมือไม่ควรทำอย่างยิ่ง รวมทั้งไม่ควรประกอบชิ้นส่วนที่แตกหักเข้าด้วยกัน โดยที่ผิวแตกหักสัมผัสกัน สิ่งเหล่านี้ไม่ช่วยต่อการวิเคราะห์แต่อย่างใด
การกัดกร่อนที่อาจจะเกิดขึ้นที่ผิวหน้าที่แตกหัก อาจจะป้องกันได้โดยพ่นด้วยอากาศอัดกระป๋องบนผิวที่แตกหัก เพื่อกำจัดสิ่งสกปรก แล้วใส่ในตู้ดูดความชื้น (Descicator) ควรหลีกเลี่ยงการเคลือบผิวหน้าที่แตกหักที่ยังไม่ได้ทำการวิเคราะห์
ส่วนผิวหน้าที่เสียหายหากสัมผัสน้ำทะเลหรือสิ่งสกปรกอื่นๆ หากจำเป็นต้องล้างผิวที่เสียหายด้วยน้ำและตามด้วยอัลกอฮอล์หรือะซิโตน เป่าให้แห้งแล้วเก็บไว้ในตู้ดูดความชื้น
การทำความสะอาดผิวหน้าที่แตกหักเพื่อส่องดูด้วยกล้องจุลทรรศน์อิเล็กตรอนแบบสแกน (SEM) ในขั้นแรกเป่าด้วยอากาศอัดกระป๋อง ล้างในอัลกอฮอล์หรืออะซีโตน ใน Ultrasonic Cleaner หรือล้างในกรดหรือด่างอ่อนๆ เพื่อกำจัดชั้นของ Corrosion ที่อยู่ที่ผิวหน้าชิ้นส่วนที่เสียหาย
การตัดชิ้นส่วนตัวอย่างที่เสียหายไปทดสอบ ควรวาดรูปอย่างคร่าวๆไว้ว่าตัดจากส่วนใด การตัดควรเป็นการตัดแบบแห้ง ในขณะตัดควรคำนึงถึงความร้อนที่เกิดขึ้น หากการตัดทำให้อุณหภูมิสูงขึ้นมาก โครงสร้างของวัสดุอาจเปลี่ยนแปลงได้ ดังนั้นจึงควรตัดห่างผิวแตกพอประมาณ หากตัดด้วยความร้อนต้องระวังไม่ให้โลหะเหลวจากการตัดไปติดที่ผิวหน้าที่แตกหักได้ การตัดแห้งดีกว่าแบบที่ใช้น้ำหล่อเย็น เพราะน้ำหล่อเย็นอาจจะกัดกร่อนผิวหน้าที่แตกหัก หรือทำให้อนุภาคที่อยู่ที่ผิวหลุดออกไปได้
5. ลำดับขั้นตอนการวิเคราะห์และการทดสอบ
การวิเคราะห์และทดสอบ จะเลือกใช้วิธีการทดสอบต่างๆ ตามความเหมาะสมในขณะนั้น โดยทั่วไปการ
ทดสอบจะมีวิธีการทดสอบต่างๆดังนี
การตรวจสอบสภาพผิวแตก (Fractography)
ระดับมหภาค (Macroscopic) โดยการใช้แว่นขยายหรือกล้อง stereo microscope ระดับจุลภาค (Microscopic) โดยการใช้ Scanning Electron Microscope (SEM) การตรวจสอบสภาพผิวแตกทำให้ทราบข้อมูลเกี่ยวกับจุดเริ่มต้นของรอยแตก ชนิด และลักษณะการขยายตัวของรอยแตก และลักษณะการแตกว่าเป็นการแตกแบบเปราะ แบบเหนียวหรือการล้าตัว เป็นต้น
การวิเคราะห์ทางเคมี (Chemical Analysis)
-การวิเคราะห์สารปนเปื้อน และผลิตภัณฑ์ที่เกิดจากการกัดกร่อน การตกผลึก (Precipitation) เพื่อวิเคราะห์หาสิ่งเจือปนที่มีอิทธิพลต่อการกัดกร่อน หรือชนิดของสารฝังใน ซึ่งจะเป็นสาเหตุให้วัสดุลดความสามารถในการรับภาระกรรม
-การวิเคราะห์ส่วนผสมของวัสดุเพื่อให้พบว่าวัสดุที่ใช้เป็นวัสดุชนิดใด เลือกใช้ถูกต้องตามข้อกำหนดที่ออกแบบไว้หรือไม่
-การวิเคราะห์องค์ประกอบของตัวกลางที่ใช้ร่วมกับชิ้นงานที่เสียหาย เพื่อหาตัวกลางที่ทำให้เกิดการกัดกร่อน
การทดสอบทางกล (Mechanical Testing)
การทดสอบความแข็ง เป็นการทดสอบทางกลที่ง่ายที่สุด ชิ้นทดสอบที่ใช้มีขนาดเล็กและไม่ต้องเตรียมชิ้นทดสอบมากนัก เมื่อเปรียบเทียบกับการทดสอบทางกลอื่นๆ ความแข็งเป็นสิ่งที่บ่งชี้ว่าชิ้นส่วนที่เสียหายผ่านกระบวนการอบชุบทางความร้อนมาตรงตามที่ระบุไว้ในข้อกำหนดของวัสดุนั้นหรือไม่ การเปรียบเทียบความแข็งชิ้นส่วนที่เสียหายกับไม่เสียหายสามารถสะท้อนถึงลักษณะการใช้งาน เช่น มี Work hardening, softening หรือมีการสูญเสียคาร์บอนที่ผิว เหล็กกล้าค่าความแข็งบริเนลล์ สามารถใช้ประมาณค่าความต้านทาทนแรงดึงได้ (Tensile strength)
UTS = 0.35 HB (เหล็กกล้ารีด)
UTS = 0.21 HB (เหล็กกล้าอบชุบ)
UTS = 0.22 HB (เหล็กกล้าผสมคาร์บอนปานกลาง)
UTS = 0.23 HB (เหล็กกล้าผสมคาร์บอนต่ำ)
(UTS คือ Ultimate Tensile Strength)
การทดสอบความต้านทานแรงดึงและแรงกระแทก การทดสอบโดยวิธีนี้ ชิ้นทดสอบต้องมีขนาดใหญ่พอสมควร ทั้งนี้เป็นไปตามมาตรฐานด้วย ในบางครั้งอาจต้องทำการทดสอบที่อุณหภูมิต่ำหรือสูงกว่าอุณหภูมิห้อง เพื่อให้สอดคล้องกับสภาพการทำงานจริง
การประเมินผลการทดสอบ หากผลการทดสอบมีค่า 5-10% ต่างไปจากค่าที่ควรเป็น (ตาม specification) ไม่ได้หมายความว่า ชิ้นส่วนนี้มีค่าความแข็งแรงลดลง หรือมีคุณภาพต่ำลงจนเป็นสาเหตุของการแตกหักได้ เพราะชิ้นทดสอบมีขนาดเล็ก ซึ่งไม่สามารถจะแทนชิ้นส่วนทั้งชิ้นได้ เช่น ชิ้นส่วนที่เสียหายอาจจะแตกหักแบบเปราะได้ที่อุณหภูมิปกติ แต่ถ้านำชิ้นส่วนมาทดสอบการกระแทกพบว่าวัสดุชนิดเดียวกันจะแตกหักที่อุณหภูมิต่ำกว่า 0 องศาเซลเซียส (ทั้งนี้ขึ้นอยู่กับคุณสมบัติของวัสดุชิ้นทดสอบด้วยว่าขึ้นอยู่กับขนาดของชิ้นทดสอบด้วยหรือไม่)
การตรวจสอบจุลโครงสร้างด้วยกล้อง Light Microscope ทำให้ได้รับข้อมูล
• Microcracks
• ขนาดและรูปร่างของเกรน (grain size)
• สิ่งเจือปน(impurity)
• การตกผลึก รูพรุน โพรงอากาศ (precipitate,porosity,blow hole)
• ลักษณะและคุณภาพของการผลิต เช่น การหล่อ การทุบ การเชื่อมต่อ การเคลือบผิว การกลึง การไส การอบชุบ เป็นต้น
การตรวจสอบแบบไม่ทำลาย เพื่อตรวจหารอยบกพร่อง เช่น รอยร้าวขนาดเล็กบนผิวชิ้นงาน และรอยบกพร่องที่มีอยู่ภายในชิ้นงาน หรือรอยแตกร้าวที่เกิดอยู่ภายในชิ้นงาน
การวิเคราะห์ความเค้นและการทดสอบจำลอง (Stress Analysis and Simulation Test)
การวิเคราะห์ความเค้นด้วยสเตรนเกจ หรือทรานดิวเซอร์ เพื่อหาภาระกรรม(Load) ที่เกิดกับชิ้นงานในขณะทำงานตามสภาวะที่ใช้งานของชิ้นงาน จะช่วยทำให้ทราบสาเหตุของความเสียหายได้
นอกจากนั้นยังมีวิธีการทำการทดสอบจำลองหลายวิธี เพื่อวิเคราะห์สาเหตุของความเสียหาย เช่น การนำชิ้นงานไปทดสอบสภาพทนต่อการกัดกร่อน (Corrosion Test) หรือการทดสอบการคืบ (Creep Test ) เป็นต้น
6. การประเมินผลและการสรุปผลวิเคราะห์
ต้องนำข้อมูลผลการวิเคราะห์ทั้งหมด รวมทั้งประวัติและข้อมูลเกี่ยวกับชิ้นงานมาประกอบกันอย่างสมเหตุสมผล บางครั้งความเสียหายอาจมีสาเหตุมาจากหลายเหตุผล ดังนั้นในการหาสาเหตุของความเสียหาย ควรแยกสาเหตุแรกหรือสาเหตุหลักออกจากสาเหตุอื่นที่อาจมีผลทำให้เกิดความเสียหายได้ง่ายขึ้นเท่านั้น
7. ข้อเสนอแนะและวิธีการแก้ไข
ข้อเสนอแนะและวิธีการแก้ไขเพื่อป้องกันความเสียหายที่เกิดขึ้นได้ในอนาคต ขึ้นอยู่กับชนิดของความเสียหาย เช่น ความเสียหายอาจเกิดเนื่องจากการติดตั้ง โครงสร้าง การออกแบบ การผลิต การใช้งาน หรือการเลือกใช้วัสดุ
ท่านสามารถศึกษาข้อมูลเพิ่มเติมได้ที่ลิงค์ด้านล่างครับ
http://www.tms.org/Students/Winners/Davidson/Davidson.html
สมัครสมาชิก:
ส่งความคิดเห็น (Atom)
การกัดกร่อนกับท่อทองแดงแบบรังมด (Ant-nest corrosion)
วันนี้มีเคสจากหน่วยงานขนส่งมวลแห่งหนึ่งแจ้งว่าท่อทองแดงในระบบเครื่องปรับอากาศเกิดการกัดกร่อนแล้วนำมาสู่การรั่วมาปรึกษา ผมจำได้ว่าเคยวิเคราะห...
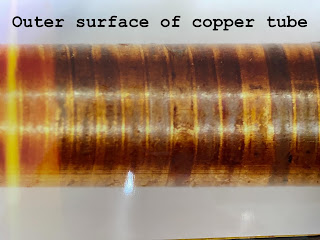
-
วันนี้เราเรียนรู้รูปแบบการเสียหายของวัสดุในรูปแบบถัดมา นั่นก็คือ การล้า หรือ Fatigue จะมีรายละเอียดเป็นอย่างไร เชิญติดตามได้เลยครับ คำว่า ...
-
cr : https://doi.org/10.1016/j.ijplas.2023.103601 เมื่อชิ้นส่วนโลหะถูกนำมาใช้งานภายใต้สภาวะอุณหภูมิสูงในขณะเดียวกันก็รับความเค้นแรงดึงไปด้ว...
-
วันนี้ผมขอนำเสนอรูปแบบการเสียหายของวัสดุแบบแรกนะครับ คือ การแตกหักแบบเปราะ การแตกแบบเปราะของวัสดุเกิดขึ้นเมื่อการกระทำของแรงทางกลมีค่าสูงก...
สติ๊กเกอร์ไลน์ ชิ้นส่วนมาตรฐาน
ตอบลบสกรูและสลักเกลียวในงานวิศวกรรม
https://store.line.me/stickershop/product/16456268
แหวนล๊อคในงานวิศวกรรม
https://store.line.me/stickershop/product/16425794
แหวนรองในงานวิศวกรรม
https://store.line.me/stickershop/product/16425165
น๊อตในงานวิศวกรรม
https://store.line.me/stickershop/product/16400172