สมัยเด็กๆ ท่านผู้อ่านบางท่านอาจจะสงสัยว่าถ่านไฟฉายหรือแบตเตอรี่มีหลักการทำงานได้อย่างไร ซึ่งหลักการทำงานดังกล่าวสามารถนำมาอธิบายการเกิดการกัดกร่อน (หรือที่เราคุ้นหูกันดีว่าการเกิดสนิม) กับเหล็กกล้าได้ เป็นที่ทราบกันดีในกลุ่มนักโลหะวิทยาว่าโครงสร้างหรือเนื้อภายในของเหล็กกล้ามีความไม่สม่ำเสมอหรือไม่เป็นเนื้อเดียวกันทั่วทั้งชิ้นงาน ไม่ว่าจะเป็นปริมาณและการกระจายตัวของสารฝังในที่ไม่ใช่โลหะ (non-metallic inclusion) ขอบเกรน (grain boundary) เฟสเฟอร์ไรต์และเพิรไลต์ ถ้าผิวหน้าเหล็กกล้าสัมผัสกับสภาวะที่มีความชื้น (อิเล็คโตรไลต์) จะทำให้เกิดกระบวนการกัดกร่อนขึ้น ซึ่งมีลักษณะเหมือนการทำงานของถ่านไฟฉายหรือแบตเตอรี่
เคยสังเกตหรือเปล่าครับว่า ในระหว่างที่ซื้อรถยนต์มาใหม่ๆ เราจะพบว่าชิ้นส่วนอุปกรณ์กันชนที่ชุบผิวด้วยโครเมียม หรืออุปกรณ์ประดับยนต์ต่างๆ สามารถเกิดสนิมขึ้นได้ ยกเว้นว่าเราจะมีการเคลือบผิว (ลงแวกซ์) ชิ้นส่วนเหล่านั้นอยู่เป็นประจำ ในปัจจุบันเราพบว่ามีการเคลือบผิวด้วยสารประเภทโครมเพื่อเพิ่มความสวยงามซึ่งมีชั้นเคลือบ 3 ชั้นคือ ทองแดง นิกเกิล และโครเมียมบนผิวหน้าเหล็กกล้า โดยพบว่าชั้นเคลือบเหล่านี้สามารถเพิ่มประสิทธิภาพในการต้านทานการกัดกร่อนจากการสัมผัสกับน้ำของเหล็กกล้าได้ดีขึ้น
ถ้าเราศึกษาเรื่องการกัดกร่อนและปฏิกิริยาทางเคมีไฟฟ้า เราจะต้องรู้จักศัพท์คำว่า EMF หรือ electro motive force ของปฏิกิริยาครึ่งเซลและลำดับกัลวานิกของแต่ละธาตุ ซึ่งในปัจจุบันได้มีการรวบรวมให้มีความทันสมัยมากขึ้นและนำมาจัดทำเป็นตารางเพื่อนำไปใช้ประโยชน์ ซึ่งเราสามารถนำไปประยุกต์ใช้ได้กับโลหะและโลหะผสมหลายชนิดรวมทั้งผิวเคลือบชนิดต่างๆ ที่สัมผัสหรือทำงานในน้ำทะเล แต่บางครั้งเราจะสังเกตเห็นว่าอนุกรมกัลวานิกจะแตกต่างกันบ้างสำหรับผู้ทำการทดสอบหรือทำการวิจัยแต่ละราย ตัวอย่างเช่น กระสุนปืนที่ทำจากทองเหลืองอาจจะมีลำดับกัลวานิกอยู่ในลำดับก่อนหน้าหรืออยู่ข้างหลังบรอนซ์ เป็นต้น ซึ่งอาจจะเกิดขึ้นกับวัสดุผสมอื่นๆ ที่อยู่ภายใต้สภาวะของสารอิเล็กโตรไลต์ที่ต่างกัน
ประเด็นของการกัดกร่อนของโลหะที่เกิดจากการสัมผัสกับสิ่งแวดล้อมที่มีน้ำเป็นองค์ประกอบ จะเกิดขึ้นก็ต่อเมื่อระบบปฏิบัติการมีองค์ประกอบของน้ำ ออกซิเจน และโลหะ (ซึ่งมีลักษณะคล้ายกับกระบวนการทำงานของแบตเตอรี่) ซึ่งเราพบว่าอุตสาหกรรมผลิตสีและการเคลือบผิวได้มีการขยายตัวในปริมาณมาก เนื่องจากความต้องการในการป้องกันการกัดกร่อนจากการสัมผัสกับน้ำของภาชนะบรรจุสารละลายที่เป็นโลหะ ผลิตภัณฑ์ที่อยู่กลางแจ้งและยวดยานทั่วไป
ประโยชน์และประสิทธิภาพของผิวเคลือบสมัยใหม่
มี 3 ปัจจัยสำคัญเกี่ยวกับกระบวนการเคลือบผิวด้วยไฟฟ้า และปัจจัยเหล่านี้สามารถนำมาประยุกต์ใช้กับกระบวนการเคลือบผิวทุกชนิด ได้แก่
1. กระบวนการเตรียมผิวหน้า
2. การควบคุมการผลิต
3. สภาพการเกาะติดของผิวเคลือบ
ปัจจัยที่เพิ่มประสิทธิภาพอื่นๆ คือการปราศจากรูพรุนและความสม่ำเสมอของความหนาผิวเคลือบ ถ้าทำการตรวจสอบภายใต้กล้องจุลทรรศน์แบบแสงที่กำลังขยายอย่างน้อย 200 เท่า จะเห็นชัดเจนว่าชั้นเคลือบโดยส่วนใหญ่จะเกาะติดอยู่บนผิวหน้าชิ้นงานเพิ่มขึ้นมาอีกชั้นหนึ่ง ดังนั้นไม่เฉพาะพันธะที่เกิดขึ้นระหว่างผิวเคลือบกับผิวหน้าชิ้นงานเท่านั้นที่ต้องควบคุม แต่การเกาะติดแต่ละชั้นเคลือบจะต้องถูกควบคุมโดยกระบวนการผลิตที่มีประสิทธิภาพเช่นกัน
การเตรียมผิวหน้า (การล้างทำความสะอาด) จะเกี่ยวกับการกำจัดสิ่งแปลกปลอม เช่นพวกออกไซด์ อนุภาคต่างๆ และคราบน้ำมัน โดยใช้ตัวทำความสะอาดประเภทอัลคาไลน์ กรดและการล้างด้วยไฟฟ้าและการเทราดอย่างทั่วถึง การทำความสะอาดที่ไม่ถูกวิธีจะมีผลต่อคุณภาพและประสิทธิภาพ โดยจะทำให้ได้พันธะการยึดเกาะที่แย่ มีผิวหยาบขนาดเล็กๆ และมีความต้านทานต่อการกัดกร่อนต่ำ ในกระบวนการที่เกี่ยวกับโลหะทั่วไปจะมีการใช้น้ำมันและจารบีค่อนข้างมาก สิ่งที่จำเป็นต้องกำจัดออกเป็นพิเศษคือสารหล่อลื่นบนผิวหน้าชิ้นงานด้วยกระบวนการที่เรียกว่า “saponification” ซึ่งเป็นปฏิกิริยาของสารไฮดรอกไซด์ที่มีค่า pH สูง (caustic) กับน้ำมันหรือจารบีแล้วกลายเป็นสบู่ที่ถูกทำละลายได้ และทำความสะอาดด้วยสาร chelating เช่น EDTA เป็นต้น เพื่อปกป้องผิวหน้าชิ้นงานที่ทำความสะอาดแล้ว
ตัวแปรด้านการควบคุมกระบวนการผลิตสำหรับการเคลือบผิวด้วยไฟฟ้า ประกอบด้วยความหนาแน่นของกระแส กำลังไฟฟ้า และความไวต่อการเกิดสารปนเปื้อน การทาสีและการเคลือบผิวด้วยสารอินทรีย์ เช่นฟิล์มโพลียูรีเทน จะไวต่อการทำละลายกับ filler mineral และความชื้น ในการตรวจสอบเบื้องต้นเราจะใช้เครื่อง FTIR เป็นเทคนิคที่ใช้ในการตรวจสอบองค์ประกอบทางเคมีของสารอินทรีย์ และเทคนิค SEM/EDS ใช้ในการจำแนก filler mineral การทดสอบการเกาะติด โดยการบิดงอชิ้นงานในมุม 180 องศา หรือขีด และลอกหรือปลอกโดยใช้เทปกาวลอกเอาผิวเคลือบออกมา ซึ่งเป็นเทคนิคการตรวจสอบและประเมินแบบทำลาย
เหตุผลในการชุบเคลือบผิวด้วยไฟฟ้าและการเคลือบผิววิธีอื่นๆ คือนอกจากเป็นการเพิ่มคุณค่าด้านความสวยงามแล้วยังเพิ่มประสิทธิภาพทางด้านความทนทานต่อการกัดกร่อนและการสึกหรอ คุณภาพและประสิทธิภาพด้านการทนทานต่อการกัดกร่อนเรานิยมประเมินด้วย ASTM Fog Tests ซึ่งจะอธิบายในตอนหลัง
การทดสอบเพื่อประเมินสภาพผิวเคลือบด้วยหมอกเกลือด้วย ASTM (ASTM Fog Test)
เป็นที่ทราบกันดีว่าการกัดกร่อนสามารถทำให้โครงสร้างทั่วๆ ไปเสียหายได้ตลอดเวลา แต่เนื่องจากอัตราการกัดกร่อนจะมีค่าที่แตกต่างกันไปตามตำแหน่งหรือทำเลที่ต่างกัน จึงเป็นการยากที่จะทำนายความเสียหายที่จะเกิดขึ้นเนื่องจากโลหะสัมผัสอยู่กับบรรยากาศต่างๆกัน โดยเฉพาะสภาวะบรรยากาศที่อยู่ใกล้ชายฝั่งทะเลหรืออยู่ในทะเลระหว่างการขนส่ง ในช่วงระยะเวลาที่ผ่านมา การทดสอบด้วยหมอกเกลือ (salt fog testing) ได้ถูกนำมาใช้ในการทดสอบเพื่อทำนายว่าโครงสร้างจะเสื่อมสภาพไปอย่างไรเมื่ออยู่ในสภาวะบรรยากาศที่มีไอเกลือเป็นองค์ประกอบ
มาตรฐานการทดสอบด้วยหมอกเกลือที่กำหนดขึ้นมาใช้ครั้งแรกในปี 1939 คือ ASTM B117 “Standard Practice for Operating Salt Spray (Fog) Apparatus” ซึ่งเป็นการทดสอบแบบเร่งให้เกิดผล เพื่อศึกษาสมบัติของวัสดุในช่วงระยะเวลาอันสั้น ซึ่งห้องปฏิบัติการอุตสาหกรรมทั่วไปได้ให้ความเชื่อมั่นในการทดสอบด้วยหมอกเกลือแบบต่างๆ เพื่อประเมินคุณภาพของสารหล่อลื่น การแทรกซึมของน้ำมัน สี กาวอุดกันรั่ว การยึดเกาะของผิวเคลือบเป็นต้น ตามข้อกำหนดของ ASTM B117-97 ได้ระบุว่าสารละลายน้ำเกลือจะมีค่า pH อยู่ในช่วงระหว่าง 6.5 – 7.2 ส่วนการทดสอบที่ค่า pH ต่ำกว่าคือทดสอบในกรดอะซิติกที่ค่า pH อยู่ในช่วง 3.1 – 3.3 เป็นข้อกำหนดของ ASTM B287 เพื่อใช้ในการประเมินผิวเคลือบสังกะสีของชิ้นงานหล่อจากแม่พิมพ์ จนกระทั่งปี 1988 ได้กำหนดเป็นมาตรฐานใหม่ขึ้นมาคือ ASTM G85-85 “Modified standard practice” ซึ่งเกิดจากการผสมผสานกันของสองมาตรฐานที่กล่าวมา ส่วนมาตรฐาน ASTM B368 CASS test ได้นำมาใช้แทนมาตรฐาน B287 โดยเพิ่มปริมาณทองแดงในสารละลายทดสอบเล็กน้อย เพื่อให้สามารถเห็นความสัมพันธ์จากการทดสอบในห้องปฏิบัติการและผลที่ได้จากการใช้งานจริงในภาคสนาม เนื่องจากการทดสอบด้วยหมอกเกลือได้มีการนำมาประยุกต์ใช้ในการตรวจสอบเป็นวงกว้าง จึงได้มีการพัฒนามาตรฐานการตรวจสอบขึ้นมาเรื่อยๆ ซึ่งมาตรฐานที่ได้กำหนดขึ้นมาใช้ใหม่ล่าสุดคือ ASTM D1735-97 condensation test ซึ่งรายละเอียดของมาตรฐานต่างๆ ที่กล่าวมาสามารถศึกษาเพิ่มเติมได้ในหนังสือ ASTM vol.03.02 และ vol.02.05
กรณีตัวอย่าง
ผลิตภัณฑ์แผ่นเหล็กกล้าม้วนได้ถูกนำมาร้องเรียนกันบ่อย โดยเฉพาะสินค้าจำพวกเหล็กแผ่นเคลือบดีบุก ซึ่งมีการเคลือบผิวอย่างดีในกระบวนการสุดท้ายด้วยพีวีซี หรือการทาสีหลายๆ ชั้นตามข้อกำหนดของมาตรฐาน
ในระหว่างการขนส่งหรือการลำเลียง วัสดุที่ห่อหุ้มอยู่ด้านนอกอาจจะถูกทำลาย มีผลทำให้น้ำทะเลสามารถแทรกซึมเข้าไปตามวัสดุที่ห่อหุ้มและรอยต่อของแผ่นเหล็กที่ม้วนติดกัน จากรายงานของผู้ตรวจสอบสินค้าพบว่าถ้าความเสียหายได้เริ่มเกิดขึ้นในทะเล จะต้องมีการเรียกร้องให้มีการตรวจสอบจากผู้ตรวจสอบอิสระ จากกรณีตัวอย่างส่วนใหญ่แล้วพบว่าปัญหาดังกล่าวจะไม่เกิดขึ้นถ้ายังไม่แกะวัสดุห่อหุ้มออก และเหล็กกล้าแผ่นที่ยังไม่ได้ม้วนที่เป็นวัสดุที่อยู่ในช่วงการผลิตเดียวกันกับที่ถูกร้องเรียนสามารถนำมาประเมินสภาพได้
สิ่งที่ผู้ทำการตรวจสอบต้องค้นหาคือความเสียหายเกิดขึ้นจากสาเหตุอะไร ไม่ว่าจะเป็นความเสียหายจากน้ำทะเล จากกระบวนการขนส่งหรือลำเลียงเหล็กแผ่นม้วนที่ไม่เหมาะสมหรือจากคุณภาพของผลิตภัณฑ์ไม่ได้มาตรฐานตั้งแต่ก่อนการผลิต หรือเงื่อนไขต่างๆ ของผลิตภัณฑ์ โดยดำเนินการตรวจสอบตามมาตรฐาน เป็นที่รู้จักกันดีว่าข้อกำหนดของ ASTM ได้นำมาใช้อย่างกว้างขวางสำหรับผลิตภัณฑ์เหล็กแผ่นม้วน รวมทั้งมาตรฐานในการบรรจุภัณฑ์หรือห่อหุ้ม การทดสอบโดยการหยดสาร (spot test) ด้วย silver nitrate บนชิ้นงานที่มีคราบเกลือเกาะติดโดยจะเปลี่ยนเป็นสีขาวประกายแวววาว สามารถนำมาใช้ในการตรวจสอบเหล็กแผ่นม้วนทั้งผิวด้านนอกและผิวด้านในที่เกิดคราบหรือมีการเปลี่ยนสี
บางครั้งการเคลือบผิวที่ไม่สมบูรณ์หลังจากกลายเป็นผลิตภัณฑ์แล้ว เช่น บริเวณขอบด้านข้างหรือวัสดุได้มีการจัดเก็บในสภาวะที่สัมผัสกับบรรยากาศทั่วๆไปเป็นเวลานาน การทดสอบวัสดุด้วยหมอกเกลือ (ASTM Fog Test) ด้วยวิธีต่างๆ สามารถนำมาใช้ในการจำลองสภาพแวดล้อมที่ใกล้เคียงกับสภาพการใช้งานจริง ถ้าการเคลือบผิวได้ถูกผลิตออกมาโดยมีจุดบกพร่องตกค้าง เกิดความเสียหายหรือปรากฏปัญหาจากกระบวนการผลิต (การยึดเกาะของชั้นเคลือบไม่ดี เกิดรอยร้าวหรือช่องว่าง) การทดสอบด้วยหมอกเกลือและการตรวจสอบทางโลหะวิทยาแล้วนำมาวิเคราะห์ จะสามารถรายงานผลที่แท้จริงและจุดเริ่มต้นของปัญหาที่เกิดขึ้นได้ แต่ถ้ามีสารเคมีที่ไม่ปกติและสงสัยว่าทำให้เกิดรอยแตก การกัดกร่อน หรือความเสียหายของแนวเชื่อม เราสามารถนำมามาตรฐานการทดสอบของ ASTM G85-94 หรืออื่นๆ หรือการทดสอบด้วยการจุ่มแช่แบบเป็นคาบหรือวัฏจักรมาใช้ในการประเมินชิ้นงานได้
ตัวแปรในการทดสอบที่สำคัญอีก 2 ชนิดที่ควรจะนำมาประเมินด้วย คืออุณหภูมิการใช้งานและค่าความเป็นกรด-ด่าง (pH) ของผลิตภัณฑ์การกัดกร่อน โดยปกติแล้วสารปนเปื้อนที่ตกค้างบนเหล็กแผ่นม้วนจะเป็นสาเหตุหลักที่ทำให้เกิดความเสียหายภาคสนามได้น้อยมาก นอกจากนั้นเราจะพบว่าผิวเคลือบไม่สามารถที่จะอยู่ยงคงกระพันได้ ซึ่งสามารถถูกทำลายได้โดยสารปนเปื้อน กระบวนการขนส่งที่ไม่ถูกต้องเหมาะสมหรือความเสียหายจากกระบวนการผลิตและการติดตั้ง
จากกรณีตัวอย่างดังกล่าวจะเห็นว่านักตรวจสอบได้ใช้เครื่องมือและเทคนิคหลากหลายในการประเมินปัญหาการกัดกร่อนของแผ่นเหล็กกล้าจากการสัมผัสกับสารละลายที่มีน้ำเป็นองค์ประกอบ และการทดสอบคุณภาพของผิวเคลือบด้วยหมอกเกลือ ดังนั้นสิ่งที่สำคัญคือจะต้องเปิดใจรับฟังปัญหาและทำการประเมินเพื่อหาแหล่งที่มาหรือต้นตอของความเสียหายของผลิตภัณฑ์ แล้วนำข้อมูลที่ได้ไปใช้ในการปรับปรุงและพัฒนาผลิตภัณฑ์ให้มีคุณภาพดีขึ้นต่อไป
ปัจจุบันห้องปฏิบัติการวิเคราะห์ความเสียหายและการกัดกร่อนของวัสดุ ของ MTEC ได้เปิดให้บริการทดสอบคุณภาพของผลิตภัณฑ์และผิวเคลือบด้วยหมอกเกลือ (salt fog test) ตาม ASTM B117 ท่านที่สนใจขอรับบริการสามารถติดต่อสอบถามรายละเอียดได้ที่เบอร์โทรศัพท์ 0 2564 6500 ต่อ 4117 และ 4736-9
เอกสารอ้างอิง
1. Practical failure analysis, vol.1 (6) December 2001.
2. ASTM handbook, vol. 03.02 and vol. 02.05.
สมัครสมาชิก:
ส่งความคิดเห็น (Atom)
การกัดกร่อนกับท่อทองแดงแบบรังมด (Ant-nest corrosion)
วันนี้มีเคสจากหน่วยงานขนส่งมวลแห่งหนึ่งแจ้งว่าท่อทองแดงในระบบเครื่องปรับอากาศเกิดการกัดกร่อนแล้วนำมาสู่การรั่วมาปรึกษา ผมจำได้ว่าเคยวิเคราะห...
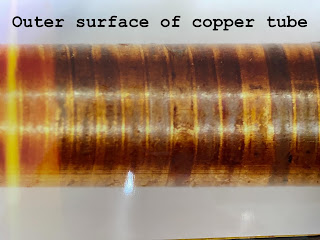
-
วันนี้เราเรียนรู้รูปแบบการเสียหายของวัสดุในรูปแบบถัดมา นั่นก็คือ การล้า หรือ Fatigue จะมีรายละเอียดเป็นอย่างไร เชิญติดตามได้เลยครับ คำว่า ...
-
cr : https://doi.org/10.1016/j.ijplas.2023.103601 เมื่อชิ้นส่วนโลหะถูกนำมาใช้งานภายใต้สภาวะอุณหภูมิสูงในขณะเดียวกันก็รับความเค้นแรงดึงไปด้ว...
-
วันนี้ผมขอนำเสนอรูปแบบการเสียหายของวัสดุแบบแรกนะครับ คือ การแตกหักแบบเปราะ การแตกแบบเปราะของวัสดุเกิดขึ้นเมื่อการกระทำของแรงทางกลมีค่าสูงก...
ขอบคุณสำหรับความรู้ที่นำมาแบ่งปันกันนะครับ ผมทำงานด้านออกแบบโครงสร้าง กำลังหาความรู้เพิ่มเกี่ยวกับเรื่องการป้องกันการกัดกร่อน ของเหล็กและคอนกรีต จากภาวะไอทะเล และไอของคาร์บอนไดออกไซด์ ถ้ามีบทความใดที่เกี่ยวข้อง ก็โปรดแนะนำด้วยนะครับ somchai_jw@yahoo.com
ตอบลบผม test เกี่ยวกับงานที่ทำการชุบอยากได้ข้อมูลของการวิเคราะห์หลังจากการ test
ตอบลบ