ท่านผู้อ่านคงทราบกันดีแล้วว่า เหล็กกล้าไร้สนิม (stainless steel) คือ เหล็กกล้าที่มีความต้านทานการกัดกร่อนสูง หรือ มีความต้านทานต่อการเกิดสนิม มากกว่า เหล็กกล้าธรรมดา (carbon steel) ซึ่งน่าจะเป็นนิยามที่เหมาะสม เพราะว่าในความเป็นจริงแล้วมันสามารถเกิดสนิมได้ การใช้เหล็กกล้าไร้สนิมจึงควรให้ความเอาใจใส่การสร้างฟิล์มบางนี้ก่อนใช้งาน เรียกว่า เทคนิค Passivation โดยการขัดฟิล์มเก่าทิ้ง หรือ ใช้กรดกัดฟิล์มเก่าทิ้งแล้วทำให้โครเมียมที่ผิวเกิดการกัดกร่อนทั่วผิวอย่างรวดเร็ว ก็จะเกิด Passive Film ได้อย่างรวดเร็ว อย่างไรก็ตาม ฟิล์มบางนี้ก็จะเกิดความเสียหายบ้างในระหว่างการใช้งาน โดยปกติ ฟิล์มบางนี้จะมีสภาพดีที่สุดถ้าใช้เหล็กกล้าไร้สนิมสัมผัสกับสารละลายที่เป็นกลางและปราศจากอิออนคลอไรด์ ถ้าสารละลายที่ใช้สัมผัสมีความเป็นกรด จะต้องพิจารณาต่อไปว่า เหล็กกล้าไร้สนิมแต่ละเกรดก็จะสามารถทนทานต่อกรดได้ไม่เท่ากัน ถ้าสารละลายมีค่า pH ต่ำกว่าค่า pHd หรือ depassivate pH ก็จะเกิดการกัดกร่อนแบบทั่วผิวหน้าขึ้นได้
นอกจากนั้น ฟิล์มบางนี้ยังจะเกิดปัญหาแตก (breakdown) ได้ในสารละลายที่มีอิออนคลอไรด์ โดยจะแตกเป็นจุดหรือ เฉพาะที่ (localized) แล้วขยายตัวเข้าไปในวัสดุ ทำให้เกิดเป็นโพรงหรือเป็นหลุม หรือเป็นรู (pitting) หรือเป็นรอยปื้น (crevice) ในเนื้อโลหะ อย่างไรก็ตาม เหล็กกล้าไร้สนิม ยังมีคุณสมบัติพิเศษ อย่างหนึ่งคือ สามารถเกิด Passive Film ซ้ำใหม่เพื่อซ่อมแซมตนเองได้ เรียกว่า Repassivate ดังนั้น โดยปกติหากเกิดการแตกของฟิล์มแล้วก็มักจะมีการเกิดฟิล์มใหม่ทับบริเวณเสียหายได้ หรือ ผู้ใช้อาจช่วยให้เกิดฟิล์มใหม่ซ้ำให้เร็วขึ้น โดยการขัดล้าง หรือใช้กรดทา แล้วล้างออกด้วยน้ำจนหมดกรด
ในกรณีที่เหล็กกล้าไร้สนิม มีความไม่ปกติในเนื้อโลหะ เช่น มีความเค้น (stress) หรือมีการตกตะกอนของคาร์ไบด์ที่ขอบเกรน (grain boundary precipitation) ตราบเท่าที่ยังมี Passive Film หุ้มอยู่ ความไม่ปกติในเนื้อโลหะจะยังไม่มีผลต่อสมบัติวัสดุ แต่หากฟิล์มเกิดละลายหรือ แตกเฉพาะจุด ก็จะเกิดการแตกร้าวเนื่องจากความเค้น (stress cracking) ได้ทั้งแบบผ่ากลางเกรนหรือไปตามเกรนได้ หรืออาจเกิดการกัดกร่อนตามขอบเกรน (intergranular corrosion) เช่น ของงานเชื่อม เป็นต้น
ปัจจุบันได้มีการค้นคว้าวิจัยหาธาตุผสมอื่นที่เติมแล้วทำให้เหล็กกล้าไร้สนิมนั้นมี Passive Film ที่ดีมากขึ้น คือ เกิดได้รวดเร็ว แข็งแรง และเกิดซ้ำได้อย่างรวดเร็ว เช่น ธาตุโมลิบดีนัม (Mo) ที่ใช้เติมลงในเกรด AISI 304 แล้วได้เป็นเกรด AISI 316 ซึ่งเป็นเกรดที่ทนทานต่อสารเคมีได้ดีกว่า เป็นต้น ดังนั้น ก่อนใช้งานเหล็กกล้าไร้สนิม จึงต้องไม่ลืมสร้าง Passive Film ให้เหมาะสมกับวัตถุประสงค์การใช้งาน และต้องหมั่นดูแล Passive Film ให้คงทนตลอดเวลาการใช้งาน
การสร้างฟิล์มคืออะไร? ถ้าพิจารณาจาก ASTM A380 จะพบว่า การสร้างฟิล์มปกป้อง (passivation) คือ “กระบวนการกำจัดเหล็กที่มาจากภายนอก (exogenous iron) หรือ สารประกอบของเหล็กจากผิวหน้าของเหล็กกล้าไร้สนิมโดยกระบวนการสลายตัวทางเคมี ซึ่งโดยทั่วไปแล้วมักดำเนินการด้วยสารละลายกรดที่สามารถกำจัดสารแปลกปลอมบนผิวหน้า แต่จะต้องไม่ส่งผลกระทบต่อเหล็กกล้าไร้สนิมเอง” ในขณะเดียวกันการสร้างฟิล์มป้องกันยังสามารถอธิบายได้อีกนัยหนึ่งว่า “เป็นกระบวนการบำบัดทางเคมีของเหล็กกล้าไร้สนิมด้วยสารออกซิแดนท์อ่อนๆ (mild oxidant) เช่น สารละลายกรดไนตริก เพื่อสร้างสภาวะที่เหมาะสมของผิวหน้าให้สามารถสร้างฟิล์มปกป้องการกัดกร่อนที่สม่ำเสมอบนผิวหน้า”
กระบวนการสร้างฟิล์มปกป้องจะกำจัดสารแปลกปลอมประเภท “free iron” ที่ตกค้างบนผิวหน้าเหล็กกล้าไร้สนิมที่อาจเกิดขึ้นระหว่างขั้นตอนกลึง ไส ขัด เจาะ หรือจากกระบวนการประกอบติดตั้ง สารแปลกปลอมเหล่านี้ถ้าไม่ถูกกำจัดออก มักจะแสดงตัวเป็นจุดเริ่มการกัดกร่อนและในที่สุดก็จะส่งผลให้เกิดการเสื่อมสภาพของชิ้นส่วน ในขณะเดียวกัน กระบวนการสร้างฟิล์มปกป้องจะส่งเสริมให้เกิดการฟอร์มฟิล์มออกไซด์ที่โปร่งแสงซึ่งบางมาก (1-5 นาโนเมตร) ซึ่งจะป้องกันเหล็กกล้าไร้สนิมไม่ให้เกิดออกซิเดชันหรือการกัดกร่อนแบบเลือก (selective oxidation) ดังนั้น จึงมักมีคำถามว่า passivation คืออะไร? เป็นการทำความสะอาดหรือเปล่า? หรือเป็นชั้นเคลือบเพื่อปกป้อง (protective coating) ของวัสดุ? คำตอบก็คือสัมพันธ์กันทั้งสองอย่าง
โดยทั่วไปแล้วกระบวนการสร้างฟิล์มมักเริ่มต้นด้วยการทำความสะอาดผิวหน้าด้วยความระมัดระวัง ทั้งนี้เพื่อกำจัดคราบน้ำมัน ไขมัน จารบี สารประกอบที่ก่อตัวขึ้น สารหล่อลื่น สารหล่อเย็น ของไหลที่ใช้ในการตัดชิ้นงาน และสิ่งแปลกปลอมทั้งเป็นสารอินทรีย์และโลหะที่อาจตกค้างจากกระบวนการประกอบติดตั้งและการกลึงไส ตัดเจาะ การกำจัดไขมันและการทำความสะอาดโดยทั่วไปสามารถดำเนินการโดย การกำจัดคราบไขมันด้วยไอน้ำ ทำความสะอาดด้วยตัวทำละลาย และ การแช่ในสารละลายด่าง เป็นต้น
หลังจากการกำจัดสารแปลกปลอมที่เป็นสารอินทรีย์และโลหะแล้ว ชิ้นส่วนจะถูกนำไปแช่ในสารละลายเพื่อสร้างฟิล์มที่เหมาะสม แม้ว่าจะมีสารละลายอยู่หลายชนิด แต่สารละลายที่นิยมใช้กันคือ กรดไนตริก แม้ว่าเมื่อไม่นานมานี้ จะมีงานวิจัยที่มีการพัฒนากระบวนการที่เป็นทางเลือกสำหรับการสร้างฟิล์มรวมทั้งสารละลายที่เป็นมิตรกับสิ่งแวดล้อมก็ตาม แต่ก็ให้ประสิทธิภาพที่เท่าเทียมกัน และแม้ว่าสารละลายทางเลือกอื่นๆ จะมีกรดซิตริกหรือสารเคมีชนิดอื่นๆ เป็นองค์ประกอบ แต่สารละลายเหล่านั้นไม่ได้รับการยอมรับในเชิงการค้าเมื่อเทียบกับสารละลายที่มีกรดไนตริกเป็นองค์ประกอบหลัก
3 ตัวแปรหลักที่จำเป็นต้องพิจารณาและควบคุมในกระบวนการสร้างฟิล์มปกป้อง ได้แก่ เวลา อุณหภูมิ และความเข้มข้น โดยข้อกำหนดทั่วไป เวลาที่ใช้ในการจุ่มแช่โดยทั่วไปจะอยู่ในช่วงระหว่าง 20 นาที ถึง 2 ชั่วโมง อุณหภูมิของอ่างโดยทั่วไปจะอยู่ในช่วงตั้งแต่อุณหภูมิห้องจนถึง 160 องศาฟาเรนไฮต์ และความเข้มข้นของกรดไนตริกจะอยู่ในช่วง 20-50% โดยปริมาตร ยกตัวอย่างเช่น
- เหล็กกล้าไร้สนิมกลุ่มออสเตนนิติก (อนุกรม 300) และมีส่วนผสมของโครเมียมมากกว่า 17% (ยกเว้น อนุกรม 440) จะใช้กรดไนตริกความเข้มข้น 20% โดยปริมาตร ที่อุณหภูมิ 50-60 C เป็นเวลา 30 นาที
- เหล็กกล้าไร้สนิมที่มีส่วนผสมของโครเมียม 12-14% และที่มีส่วนผสมของคารบอนสูง/โครเมียมสูง( อนุกรม 440) จะใช้กรดไนตริกความเข้มข้น 20% โดยปริมาตร ผสมกับสารละลายโซเดียมไดโครเมท ที่อุณหภูมิ 50-60 C เป็นเวลา 30 นาที
- เหล็กกล้าไร้สนิมกลุ่มทำให้แข็งโดยการตกตะกอน (Precipitation Hardening Stainless Steel) จะใช้กรดไนตริกความเข้มข้น 50% โดยปริมาตร ที่อุณหภูมิ 50-60 C เป็นเวลา 30 นาที
อาจมีบางข้อกำหนดที่เลือกใช้ sodium dichromate เป็นส่วนผสมในสารละลายสร้างฟิล์ม หรือใช้ล้างทำความสะอาดก่อนการสร้างฟิล์ม เพื่อช่วยให้เกิดการฟอร์มฟิล์มโครมิกออกไซด์ (chromic oxide film) การควบคุมสารละลายควรกระทำอย่างระมัดระวังโดยต้องควบคุมความบริสุทธิ์ของน้ำ สารแปลกปลอมเชิงโลหะ (metallic impurities) ในระดับ ppm (parts per million) และปรับเปลี่ยนสารเคมีเมื่อมีความเข้มข้นเปลี่ยนไป ซึ่งจะส่งผลให้ฟิล์มที่เกิดขึ้นมีประสิทธิภาพที่ดี ชนิดของเหล็กกล้าไร้สนิมที่จะใช้ในกระบวนการสร้างฟิล์มก็เป็นอีกปัจจัยหนึ่งที่ต้องพิจารณาเมื่อทำการเลือกกระบวนการสร้างฟิล์มที่ให้ประสิทธิภาพมากที่สุด การเลือกอ่าง (เวลา, อุณหภูมิ และ ความเข้มข้น) ก็เป็นตัวแปรที่ต้องพิจารณาเพื่อให้เหมาะสมกับโลหะผสมแต่ละชนิด ดังนั้นความรู้เกี่ยวกับชนิดของวัสดุและกระบวนการสร้างฟิล์มเป็นสิ่งที่สำคัญยิ่งต่อประสิทธิผลที่ต้องการ ในทางกลับกัน การเลือกอ่างที่ไม่ถูกต้อง รวมทั้งการเลือกกระบวนการ และ/หรือการควบคุมกระบวนการที่ไม่เหมาะสมมักส่งผลให้ได้ผลที่ไม่สามารถยอบรับได้ และบางครั้งอาจนำไปสู่ความเสียหายที่รุนแรงตามมาได้ ยกตัวอย่างเช่น เกิดรูเข็มอย่างรุนแรง มีการกัดผิวหน้าหรือทำลายทั่วทั้งผิวหน้าของชิ้นส่วน
อุปกรณ์และข้อควรระวัง
กระบวนการสร้างฟิล์มปกป้องบนผิวหน้าเหล็กกล้าไร้สนิมจะได้ประสิทธิภาพที่ดี เมื่อช่างเทคนิคและผู้ที่เกี่ยวข้องได้ผ่านการฝึกอบรม มีประสบการณ์และคุ้นเคยกับสารอันตรายทางวิทยาศาสตร์ โดยต้องเข้าใจอย่างดีเกี่ยวกับความปลอดภัยในระหว่างการสร้างฟิล์ม ซึ่งจำเป็นต้องมีการสวมรองเท้าบูทพิเศษ ถุงมือ มีการใช้ผ้ากันเปื้อนและอุปกรณ์ความปลอดภัยอื่นๆ มีการจัดเตรียมแทงค์ อุปกรณ์ให้ความร้อน และระบบระบายอากาศ รวมทั้งตะกร้าและชั้นวางของ โดยจะต้องออกแบบให้เหมาะสมกับการดำเนินการ เหล็กหรือชิ้นส่วนที่เป็นเหล็กหรืออุปกรณ์ต่างๆ จะต้องไม่นำมาใช้ในกระบวนการ ยิ่งไปกว่านั้น เพื่อให้สนองต่อความต้องการของสังคมที่ต้องการกระบวนการที่เป็นมิตรกับสิ่งแวดล้อมแล้ว น้ำและอากาศที่ใช้ในกระบวนการรวมทั้งระบบต่างๆ ควรจะมีการติดตั้งอยู่ด้วย
ข้อกำหนดและการทวนสอบ
มีข้อกำหนดที่ได้รับการยอมรับทั่วไปจากอุตสาหกรรมอยู่ส่วนหนึ่งเมื่อจะใช้ในการอ้างอิงเพื่อเลือกกระบวนการสร้างฟิล์ม ซึ่งเขามักสนใจข้อมูลเกี่ยวเวลา อุณหภูมิ และความเข้มข้นในระหว่างกระบวนการสร้างฟิล์ม และความต้องการในการทดสอบในลำดับถัดมา เพื่อตรวจสอบประสิทธิภาพของกระบวนการ องค์กรขนาดใหญ่หลายแห่งมักมีการพัฒนาข้อกำหนดขึ้นไว้ใช้เป็นการภายใน เพื่อควบคุมความต้องการเฉพาะของพวกเขาเกี่ยวกับการทวนสอบกระบวนการสร้างฟิล์ม ซึ่งในสถานการณ์เช่นนั้นมักจะระมัดระวังในการอ้างอิงขั้นตอนการพิสูจน์เพื่อเมื่อชิ้นส่วนมีการสร้างฟิล์ม จากการอ้างอิงข้อกำหนด นั้นอาจกล่าวได้ว่าไม่จำเป็นต้องไปเปลี่ยนแปลงอะไรเนื่องจากมันดีอยู่แล้ว และโดยจากการใช้ประสบการณ์ที่ผ่านมาของคนอื่นทั้งความสำเร็จและความล้มเหลว ทำให้เราสามารถกำจัดงานที่นอกเหนือความคาดหมายที่อาจมากับกระบวนการใหม่
ปัจจุบันนี้มีมาตรฐานที่นิยมใช้กัน คือ ASTM A-967 และ ASTM A-380 ซึ่งทั้ง 2 มาตรฐานได้เขียนไว้อย่างดี ให้รายละเอียดที่ชัดเจนเกี่ยวกับคำแนะนำในกระบวนการทั้งหมด ตั้งแต่กระบวนการผลิตจนถึงความต้องการการทดสอบในขั้นตอนสุดท้าย หากเจ้าของงานไม่แน่ใจว่าต้องการอะไร ก็สามารถใช้อ้างอิงได้ทั้งหมดหรือเพียงบางส่วนก็ได้ ความต้องการในการทดสอบสามารถที่จะใช้หรือยกเว้นก็ได้ ทั้งนี้ขึ้นอยู่กับสถานการณ์ แต่มีข้อกำหนดในการทวนสอบอยู่ข้อหนึ่งที่นิยมใช้กันมากก็คือ การทดสอบด้วยคอปเปอร์ซัลเฟต โดยชิ้นส่วนที่ผ่านการสร้างฟิล์มจะถูกจุ่มแช่ในสารละลายคอปเปอร์ซัลเฟต 6 นาที ล้างน้ำสะอาดและทำการตรวจสอบด้วยสายตา โดยถ้าพบว่าผิวหน้ามีลักษณะเป็นชมพู (ทองแดง) จะแสดงให้เห็นว่าผิวหน้าวัสดุมีการเหล็กอิสระเป็นสารแปลกปลอมตกค้าง ลักษณะดังกล่าวชี้ให้เห็นว่าไม่สามารถยอมรับได้ นอกจากนี้ยังมีการทวนสอบอื่นๆ ได้แก่ การทดสอบด้วยหมอกเกลือเป็นเวลา 2 ชั่วโมง หรือทดสอบในสภาวะที่มีความชื้นสูง 24 ชั่วโมง การทดสอบดังกล่าวสามารถดำเนินการได้โดยการนำชิ้นส่วนที่ผ่านการสร้างฟิล์มเข้าไปไว้ในภาชนะที่ควบคุมมิดชิดเป็นอย่างดีที่สามารถสร้างสภาวะสิ่งแวดล้อมให้เร่งการกัดกร่อนได้ หลังจากชิ้นงานได้สัมผัสกับสิ่งแวดล้อมที่กัดกร่อนตามระยะเวลาที่กำหนดแล้ว ก็จะนำชิ้นส่วนออกมาและนำไปประเมิน ซึ่งมาตรฐานที่นิยมใช้กัน คือ ASTM B-117 เพราะเป็นการทดสอบที่ใช้อ้างอิงและเป็นที่ยอมรับ แต่สิ่งที่เราทราบอีกอย่างหนึ่ง คือ การทดสอบแต่ละอย่างมีข้อดีและข้อจำกัดกันอย่างไรบ้าง ดังนั้นโปรดใช้ความระมัดระวังในการเลือกวิธีการทดสอบที่เหมาะสม ซึ่งพิจารณาจากชนิดของโลหะผสมและสิ่งแวดล้อมที่นำไปใช้งาน
การพิสูจน์ทราบถึงการเกิดขึ้นของฟิล์ม และความเสถียรของฟิล์มค่า pHd ความสามารถในการสร้างฟิล์มใหม่ (Repassivation) และอื่นๆ สามารถทำได้โดยวิธีทางเคมีไฟฟ้า ซึ่งเป็นวิธีที่ทันสมัย ให้ข้อมูลได้มาก และปลอดภัยต่อสิ่งแวดล้อม
การขึ้นรูปทางกลและกระบวนการทางความร้อน
บางครั้งเราอาจจะมองข้ามตัวแปรที่ส่งผลเชิงลบต่อการกระบวนการสร้างฟิล์ม คือ กระบวนการขึ้นรูปทางกลและการปฏิบัติการทางความร้อนที่ไม่ดี โดยมักอยู่ในรูปของสารตกค้างที่เกิดขึ้นระหว่างกระบวนการผลิตและ/หรือระหว่างกระบวนการทางความร้อน ปัจจัยเหล่านี้จะนำไปสู่ผลการทดสอบที่ไม่สามารถยอมรับได้ ดังนั้นการปฏิบัติดังต่อไปนี้จะช่วยลดสารตกค้างระหว่างกระบวนการผลิต และเพิ่มประสิทธิภาพในการสร้างฟิล์มและผลการทดสอบที่ได้รับการยอมรับ:
• ไม่ควรใช้จานขัด วัสดุขัด หรือแปรงลดที่ทำจากเหล็ก เหล็กออกไซด์ เหล็กกล้า สังกะสี หรือ วัสดุอื่นที่สามารถเหนี่ยวนำให้เกิดเป็นสารแปลกปลอมตกค้างบนผิวหน้าเหล็กกล้าไร้สนิม
• ถ้าเป็นไปได้แนะนำให้ใช้เครื่องมือที่เป็นคาร์ไบด์หรือพวกอโลหะต่างๆ
• ไม่ควรใช้จานขัด หินเจียร และแปรงลวดที่ผ่านการใช้งานกับโลหะชนิดอื่นมาก่อนมาใช้กับเหล็กกล้าไร้สนิม
• ให้ใช้อุปกรณ์ขัดที่ยังไม่ใช้งาน เช่น ลูกปัดแก้ว หรือซิลิกาที่ไม่เจือเหล็ก หรือทรายอลูมิน่าสำหรับทำความสะอาดผิวหน้า ไม่ควรใช้เม็ดเหล็กกล้าหรือสารขัดที่ผ่านการขัดกับวัสดุชนิดอื่นมาก่อน
• ทำความสะอาดอย่างระมัดระวังก่อนน้ำชิ้นส่วนเข้าสู่กระบวนการทางความร้อน การอบคลายความเค้น การอบอ่อน การดึง หรือกระบวนการขึ้นรูปทางความร้อนอื่นๆ ที่สามารถส่งเสริมให้เกิดสารตกค้างฝังลึกลงไปบนผิวหน้าชิ้นงาน อันส่งผลให้ไม่สามารถกำจัดออกได้ในระหว่างกระบวนการสร้างฟิล์ม
• ควรระมัดระวังในการดำเนินการระหว่างกระบวนการทางความร้อนทั้งหมด ทั้งนี้เพื่อหลีกเลี่ยงการฟอร์มตัวของออกไซด์หรือการเปลี่ยนสีบนผิวหน้า (discoloration) การสร้างฟิล์มไม่ได้ออกแบบเพื่อกำจัดลักษณะการเปลี่ยนสีที่เกิดขึ้นบนผิวหน้าชิ้นงาน และจะไม่ซึมลึกเข้าไปในชั้นออกไซด์ที่หนา ในสถานการณ์ที่รุนแรง อาจจะเพิ่มขั้นตอนการล้างด้วยกรดเพื่อกำจัดคราบออกไซด์ (pickling and descaling) ก่อนกระบวนการสร้างฟิล์มเพื่อกำจัดลักษณะการเปลี่ยนสีที่เกิดขึ้นบนผิวหน้า ควรควบคุมบรรยากาศภายในเตาอบของทุกกระบวนการทางความร้อนเป็นอย่างดีเพื่อลดการเกิดสารตกค้างที่มากับบรรยากาศ และต้านทานการเกิดออกไซด์ เมื่อสามารถดำเนินการได้ตามคำแนะนำดังกล่าว ชิ้นส่วนเหล็กกล้าไร้สนิมก็จะมีสมบัติต้านทานการเกิดสนิม
สรุป
จากข้อมูลที่กล่าวมา ผู้อ่านคงทราบแล้วว่าประสิทธิภาพที่ดีของโลหะผสมที่เราเสียค่าใช้จ่ายมาค่อนสูงนั้น เราจะดำเนินการอย่างไร การสร้างฟิล์มของเหล็กกล้าไร้สนิมเป็นกระบวนการที่เป็นทั้งศาสตร์และศิลป์นั้น เราต้องควบคุมกระบวนการขึ้นรูปทางกล การประกอบติดตั้ง และการปฏิบัติการทางความร้อนอย่างใกล้ชิด เนื่องสามารถส่งผลกระทบต่อสมบัติความต้านทานการกัดกร่อนของชิ้นส่วนได้ เป็นที่ทราบกันดีว่า การสร้างฟิล์มบนผิวหน้าเหล็กกล้าไร้สนิมจะทำให้มีสมบัติต้านทานการกัดกร่อน แต่ควรตระหนักถึงประสิทธิภาพสูงสุดของโลหะผสมเหล่านี้ โดยผู้ที่เกี่ยวข้องทุกภาคส่วนที่เกี่ยวข้องกับการผลิตจะต้องเข้าใจถึงความรับผิดชอบต่อหน้าที่เพื่อให้เกิดความสมบูรณ์ของวัสดุตลอดกระบวนการสร้างฟิล์ม
เอกสารอ้างอิง
1. ASTM A 380 - 96 Standard Practice for Cleaning, Descaling, and Passivation of Stainless Steel Parts, Equipment, and Systems
2. ASTM A 967 - 96 Standard Specification for Chemical Passivation Treatments for Stainless Steel Parts
3. ASTM B 117 - 95 Standard Practices for Operating Salt Spray (Fog) Apparatus
สมัครสมาชิก:
ส่งความคิดเห็น (Atom)
การกัดกร่อนกับท่อทองแดงแบบรังมด (Ant-nest corrosion)
วันนี้มีเคสจากหน่วยงานขนส่งมวลแห่งหนึ่งแจ้งว่าท่อทองแดงในระบบเครื่องปรับอากาศเกิดการกัดกร่อนแล้วนำมาสู่การรั่วมาปรึกษา ผมจำได้ว่าเคยวิเคราะห...
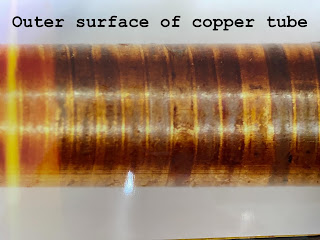
-
วันนี้เราเรียนรู้รูปแบบการเสียหายของวัสดุในรูปแบบถัดมา นั่นก็คือ การล้า หรือ Fatigue จะมีรายละเอียดเป็นอย่างไร เชิญติดตามได้เลยครับ คำว่า ...
-
cr : https://doi.org/10.1016/j.ijplas.2023.103601 เมื่อชิ้นส่วนโลหะถูกนำมาใช้งานภายใต้สภาวะอุณหภูมิสูงในขณะเดียวกันก็รับความเค้นแรงดึงไปด้ว...
-
วันนี้ขอนำเสนอรูปแบบการเสียหายของวัสดุแบบที่ 2 คือ การเสียหายแบบเหนียว วัสดุเหนียวที่ถูกใช้งานภายใต้สภาวะการรับความเค้นแรงดึง (Tensile Str...
สวัสดีครับ ผมชื่อ อรรถพล เป็น Sales Engineer จากบริษัท AGMA PACIFIC ENGINEERING ครับ
ตอบลบเป็นบริษัทนำเข้าเทคโนโลยีเกี่ยวกับ Surface Treatment เข้ามาในประเทศไทย
เนื่องจากกระผมจบใหม่และกำลังหาความรู้เกี่ยวกับ Passivation และ Phosphating เพื่อใช้ในการทำงาน
ต้องขอขอบคุณอย่างยิ่งสำหรับบทความนี้ครับ
ป.ล.ไม่ทราบว่ามีบทความเกี่ยวกับกระบวนการ Phosphating บ้างหรือปล่าวครับ ผมยังสับสนอยู่ ถ้ามีให้อ่านเพื่อเป็นองค์ความรู้บ้าง จะขอบคุณเป็นอย่างยิ่งเลยครับ
อรรถพล ใจสุข
Sales Engineer for ST&F unit
AGMA Pacific Engineering Co., Ltd
www.agmapacific.com
Tel. +66(0)2 6793 260, +66(08)7 9815 731, Fax. +66(0)2 2863 31
I read your post and I found this is amazing. Your thought process is wonderful. The way you express yourself is awesome.
ตอบลบCustom Precision Manufacturer
การล้างกรดเพื่อกำจัดคราบอ็อกไซด์หรือรอยไม้จากการเชื่อม (pickling) เป็นขั้นตอนที่สำคัญก่อนการสร้างฟิล์ม โดยทั่วไป จะทำใน ลักษณะใดลักษณะหนึ่ง ดังต่อไปนี้ 1. การกัดกรดโดยจุ่มแช่ ในถัง หรือ tank immersion pickling 2. การกัดกรดโดยการฉีดพ่นน้ำยา หรือ spray pickling 3. การกัดกรดโดยการไหลวนน้ำยา หรือ circulation pickling วิธีที่ปลอดภัยที่สุดได้แก่ การกัดกรดโดยการจุ่มแช่ แต่มีข้อเสียคือไม่สามารถทำที่หน้างานได้ ต้องทำที่โรงงานเท่านั้น วิธีสเปรย์สามารถใช้ที่หน้างานได้แต่ต้องมีระบบความปลอดภัยป้องกันอันตรายจากสารเคมีในขณะฉีดพ่น ส่วน การไหลเวียนน้ำยา เหมาะที่จะใช้กับสเตนเลสที่เป็นระบบท่อ อย่างกรณีของลูกค้าที่ซื้อน้ำยากัดกรด หรือ pickling dip solution ของเราไปใช้ นำไปใช้กับการกัดกรดแบบจุ่มแช่ ครับ มีการควบคุมเงื่อนไข เวลา และอุณหภูมิการแช่เพื่อให้ได้ผลการขจัดคราบที่ดีที่สุด เคมีที่เราออกแบบมีประสิทธิภาพในการใช้งานไม่ต่างจากน้ำยาราคาแพงของต่างประเทศ สนใจติดต่อมาได้นะครับ ชินวุฒิ โทร 0818843207 หจก.อินทิเกรท ซายน์ครับ
ตอบลบหลังจากทำ passavasion แล้ว ผมจะทราบได้อย่างไร ว่า สแตนเลส นั้น เกิดชั้นฟิล์มแล้ว มีวิธีตรวจสอบอย่างไร เช่นงานท่อที่มีขนาดเล็กๆ 1/2", 3/4",1"
ลบบริการทำความสะอาดและปรับพื้นผิว (Passivation) ท่อและถังบรรจุภัณฑ์
ตอบลบ• ถังเก็บผลิตภัณฑ์ นม น้ำผลไม้ น้ำปลา ยาสระผม ครีมนวด และอื่น
• ท่อผลิตภัณฑ์ นม น้ำมผลไม้ น้ำปลา ยากสะผม ครีมนวด และอื่นๆ
• ชิ้นงาน ในกระบวนการผลิตที่เกิดสนิม ต้องการทำความสะอาด เช่น Fin air, Condenser, Fin fan, Boiler
ติดต่อ เอ็ก
PEG Industrial Services Co.,Ltd
Tel : 091-992-9242
Line : sutthipeera
email: sutthiroj.p@peg.in.th