ข้อได้เปรียบของการตรวจสอบแบบไม่ทำลายมีดังนี้
1. สามารถทำการตรวจสอบได้โดยไม่ทำให้เกิดความเสียหายใดๆ กับชิ้นงาน ดังนั้นหลังการตรวจสอบจึงสามารถนำชิ้นงานกลับมาใช้ได้อีกสำหรับชิ้นส่วนที่อยู่ในเกณฑ์ยอมรับได้
2. สามารถทำการตรวจสอบทุกชิ้นงาน (100%) และแบบสุ่มตัวอย่าง (random)
3. ใช้ในการร่วมตรวจสอบซึ่งอาจมีหลายชนิดกับงานชิ้นเดียวกันได้เพื่อตรวจสอบความถูกต้องของการตรวจสอบ
4. สามารถทำการตรวจสอบซ้ำกับชิ้นงานเดิมได้
5. สามารถตรวจสอบชิ้นงานขณะใช้งานได้ (ใช้ได้ในบางวิธีการ) โดยไม่จำเป็นต้องหยุดทำงาน
6. สามารถตรวจสอบชิ้นงานตามระยะเวลาการใช้งานได้ จึงทำให้ทราบการเปลี่ยนแปลงสภาพของชิ้นงานหลังผ่านการใช้งานแล้ว
7. มีอุปกรณ์ที่ใช้ในงานภาคสนามได้สะดวก
8. ในการตรวจสอบชิ้นงานที่เหมือนกัน อาจออกแบบการตรวจสอบให้เป็นระบบอัตโนมัติได้
9. ไม่ต้องเตรียมชิ้นงานเพื่อการตรวจสอบหรือบางครั้งอาจทำเพียงเล็กน้อย
วันพฤหัสบดีที่ 11 สิงหาคม พ.ศ. 2554
วันพฤหัสบดีที่ 4 สิงหาคม พ.ศ. 2554
การทดสอบการล้าตัวของล้ออัลลอยด์ (Fatigue strength testing of alloy wheel)
เป็นที่ทราบกันดีว่าล้ออัลลอยด์ที่นิมใช้กันในปัจจุบันนั้นส่วนใหญ่มักใช้โลหะอะลูมิเนียมผสม (aluminum alloy) ในการผลิตด้วยกระบวนการ die casting ซึ่งเป็นที่ทราบกันอีกว่า ถ้ามีควบคุมคุณภาพในการผลิตไม่ดีจะส่งผลให้เกิดจุดบกพร่องภายใน (internal defect) ได้ ไม่ว่าจะเป็นฟองอากาศ (porosity) โพรงหดตัว (shrinkage) ห่อฟิล์ม (film folding) เป็นต้น ซึ่งจุดบกพร่องเหล่านี้สามารถตรวจสอบได้โดยเทคนิคการฉายรังสี (radioscopic inspection)
เนื่องจากล้อแม็กต้องรับแรงแบบคาบ (cyclic load) ตลอดเวลาในระหว่างที่รถวิ่ง ดังนั้น เพื่อให้เกิดความมั่นใจกับผู้ขับขี่หรือเพื่อเพิ่มความเชื่อมั่นให้กับลูกค้า ผู้ผลิตบางรายอาจนำไปทดสอบการล้าตัว (Fatigue Testing) เนื่องจากโลหะอะลูมิเนียมผสมไม่สามารถทดสอบหา endurance limit ได้เหมือนกับชิ้นส่วนที่เป็นเหล็กกล้า แต่สามารถทดสอบเพื่อหา fatigue strength ได้
โดยเบื้องต้นจะตัดชิ้นงานออกจากล้อแม็ก (ภาพ A) จากนั้นนำไปเตรียมชิ้นส่วนทดสอบ (ภาพ B) เมื่อทำการทดสอบเสร็จจะได้จำนวนรอบที่ชิ้นงานทดสอบสามารถทนได้ก่อนเกิดการแตกหัก
บางครั้งพบว่าชิ้นงานทดสอบอาจสามารถรับแรงแบบคาบได้ถึงหมื่นรอบ ดังนั้น เราจำเป็นต้องศึกษาผิวหน้าแตกหัก (Fracture surface analysis) เพื่อหาลักษณะเฉพาะที่ส่งเสริมให้วัสดุแตกหักได้ง่าย ดังตัวอย่างในภาพ C จะพบว่า ผิวหน้าแตกหักสามารถแบ่งได้เป็น 2 โซน กล่าว โซนที่เกิดการแตกหักจากการล้าตัว (fatigue zone; FZ) ซึ่งในโซนดังกล่าวจะมีจุดเริ่มรอยแตก (fracture origin) ให้เห็น เมื่อทำการตรวจสอบที่กำลังขยายสูงด้วย SEM จะพบจุดบกพร่องที่เป็นสาเหตุของการแตกหัก ซึ่งตัวอย่างในภาพ D จะพบจุดบกพร่องจาก die casting process ซึ่งจุดบกพร่องเหล่านี้สามารถลดได้ ท่านใดอยากทราบ โปรดติดตามตอนต่อไปนะครับ............................
เนื่องจากล้อแม็กต้องรับแรงแบบคาบ (cyclic load) ตลอดเวลาในระหว่างที่รถวิ่ง ดังนั้น เพื่อให้เกิดความมั่นใจกับผู้ขับขี่หรือเพื่อเพิ่มความเชื่อมั่นให้กับลูกค้า ผู้ผลิตบางรายอาจนำไปทดสอบการล้าตัว (Fatigue Testing) เนื่องจากโลหะอะลูมิเนียมผสมไม่สามารถทดสอบหา endurance limit ได้เหมือนกับชิ้นส่วนที่เป็นเหล็กกล้า แต่สามารถทดสอบเพื่อหา fatigue strength ได้
โดยเบื้องต้นจะตัดชิ้นงานออกจากล้อแม็ก (ภาพ A) จากนั้นนำไปเตรียมชิ้นส่วนทดสอบ (ภาพ B) เมื่อทำการทดสอบเสร็จจะได้จำนวนรอบที่ชิ้นงานทดสอบสามารถทนได้ก่อนเกิดการแตกหัก
บางครั้งพบว่าชิ้นงานทดสอบอาจสามารถรับแรงแบบคาบได้ถึงหมื่นรอบ ดังนั้น เราจำเป็นต้องศึกษาผิวหน้าแตกหัก (Fracture surface analysis) เพื่อหาลักษณะเฉพาะที่ส่งเสริมให้วัสดุแตกหักได้ง่าย ดังตัวอย่างในภาพ C จะพบว่า ผิวหน้าแตกหักสามารถแบ่งได้เป็น 2 โซน กล่าว โซนที่เกิดการแตกหักจากการล้าตัว (fatigue zone; FZ) ซึ่งในโซนดังกล่าวจะมีจุดเริ่มรอยแตก (fracture origin) ให้เห็น เมื่อทำการตรวจสอบที่กำลังขยายสูงด้วย SEM จะพบจุดบกพร่องที่เป็นสาเหตุของการแตกหัก ซึ่งตัวอย่างในภาพ D จะพบจุดบกพร่องจาก die casting process ซึ่งจุดบกพร่องเหล่านี้สามารถลดได้ ท่านใดอยากทราบ โปรดติดตามตอนต่อไปนะครับ............................
สมัครสมาชิก:
บทความ (Atom)
การกัดกร่อนกับท่อทองแดงแบบรังมด (Ant-nest corrosion)
วันนี้มีเคสจากหน่วยงานขนส่งมวลแห่งหนึ่งแจ้งว่าท่อทองแดงในระบบเครื่องปรับอากาศเกิดการกัดกร่อนแล้วนำมาสู่การรั่วมาปรึกษา ผมจำได้ว่าเคยวิเคราะห...
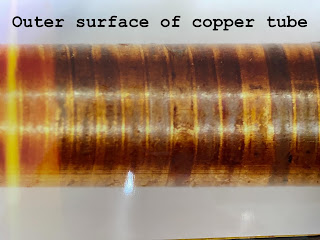
-
วันนี้เราเรียนรู้รูปแบบการเสียหายของวัสดุในรูปแบบถัดมา นั่นก็คือ การล้า หรือ Fatigue จะมีรายละเอียดเป็นอย่างไร เชิญติดตามได้เลยครับ คำว่า ...
-
cr : https://doi.org/10.1016/j.ijplas.2023.103601 เมื่อชิ้นส่วนโลหะถูกนำมาใช้งานภายใต้สภาวะอุณหภูมิสูงในขณะเดียวกันก็รับความเค้นแรงดึงไปด้ว...
-
วันนี้ขอนำเสนอรูปแบบการเสียหายของวัสดุแบบที่ 2 คือ การเสียหายแบบเหนียว วัสดุเหนียวที่ถูกใช้งานภายใต้สภาวะการรับความเค้นแรงดึง (Tensile Str...